Total Quality Management Research Guides Postharvest Quality Success
Research Update August 2022, powered by FloraLife
Terril A. Nell – Professor of Floriculture Emeritus University of Florida

Flower losses of 20 – 30% are reported as flowers move from growers to retail outlets and to consumers. High quality, long-lasting flowers are among the highest priorities when consumers make floral purchases. Imagine the impact on your profit if you could reduce your shrink to 5% or less. Well, you can! Care and handling research in the U.S., Europe, Israel, and other countries has provided guidelines for maintaining long lasting flowers.
So, why do we still experience high flowers losses, reduced quality, and short vase life? Care and handling practices may sound simple, but how you integrate them into your business routines can make all the difference.
Some years ago, an American engineer who focused on business practices and management established ‘Total Quality Management’ (TQM)—an approach that transformed industrial processes and reduced shrink significantly in the automobile and electronics industries. If these industries can benefit from TQM, so can the flower industry. TQM is a management system that:
- is customer-focused
- involves every employee in a quality improvement culture
- quantifies success
- leads to continual improvement
Establish a Routine Employee Training Program for Total Quality Management
A complete set of care and handling guidelines should be developed for your company. The care and handling guidelines below can be the basis for the training and maintenance of best practices.
The focus should be on producing a high-quality product and reducing waste. Your company should have a way of monitoring success by having employees perform the key steps and maintain compliance records.
Let’s review the critical care and handling elements. The University of Florida flower postharvest program evaluated and refined these practices over a 15-year period. We evaluated every step in the logistics chain to be sure the best practices were proven to be effective.
Purchase The Longest-Lasting Varieties
Think about it – as consumers we may purchase automobiles, electronics, kitchen appliances and clothing/shoes on appearance and brand rather than considering the facts about the performance and life of these products. The same is true with flowers. Longevity, quality, and performance are the criteria used to select flower varieties. Not every red rose, yellow chrysanthemum or pink alstroemeria lasts the same number of days. Some may last but have leaves that turn yellow, buds that drop or flowers that fail to open. Assign someone to track these qualities. If you see consistent problems with a variety, cross that one off your list and choose another variety that performs better.
Sanitation and Flower Processing
Once flowers arrive, a TQM care and handling program must be directed toward cleanliness and keeping flowers hydrated with the proper solutions. Ideally one person will be responsible for processing and this responsibility should be recognized and respected by all other employees. The individual should be responsible for:
- Receiving and inspecting flowers for insects and diseases.
- Washing buckets before use with an anti-bacterial product such as FloraLife® D.C.D.® Cleaner.
- Using clean water, not recycled water (Image 1).
- Cutting stems with a clean, sharp knife (or not cutting if using FloraLife® Express Technology solutions).
- Selecting the correct hydration and flower food solution and dosing & mixing it properly. Growers and wholesaler should use commercial hydration solutions and retail outlets should use flower foods (Image 2).
- Place flowers in the cooler and maintain temperature at 34 – 38 F (1-3C) and 80% humidity. Keep a written record of these measurements three times daily.
Cleanliness of floors, workspaces and cooler
Assign a person to monitor cleanliness practices. Tables should be disinfected after every arrangement is completed. Although a single person assumes the responsibility for monitoring, each employee should be responsible for his/her work area. Diseases can remain on unclean surfaces for days, if not longer.
Floors of coolers should be swept daily. Shelving and tables in coolers should be disinfected every two weeks, recorded with the date and initials of the person responsible. Cooler walls should be wiped down monthly with an anti-fungal disinfectant. Again, record-keeping assures accountability.
Floral Designers Responsibilities
New employees should understand the importance of sanitation, and make a commitment to routine application of practices to minimize contamination:
- Using an antifungal dip to sanitize knives and clippers between each floral design.
- Wiping table down after each design.
- Coordinating with flower processing staff to have properly mixed flower food for arrangements.
- Including flower food packets with arrangements or bouquets.
Continual Improvement
Everyone in the organization should be striving to achieve customer satisfaction. The tone is set by top management and spreads down into the organization, by establishing standard practices and engaging every employee in a process of continual improvement. Employees should be empowered (and rewarded) for suggestions that lead to less waste and greater profitability for the company. TQM recognizes the “Pareto Principle”—that 80% of the problems come from 20% of the causes. If your team can identify those causes, and correct them, then continual improvement will occur in your business.
Conclusion
Widely accepted care and handling practices have been proven to reduce flower losses significantly. TQM is a tool you can use in your business to ensure that these practices are being consistently applied.
A quick summary of Total Quality Management and Flower Care and Handling:
Key elements of a Total Quality Management for Flowers
- Define your quality goals
- Quantify your care and handling protocols
- Educate employees regularly
- Develop a quality improvement culture
- Gather data for fact-based decision-making
- Foster opportunities for continuous improvement
Critical Care and Handling Elements
- Select the best varieties
- Keep all tools and facilities clean and sanitized
- Keep flowers hydrated
- Use clean water
- Use effective commercial hydration and flower food solutions
- Maintain cold conditions
- Provide customers with flower food
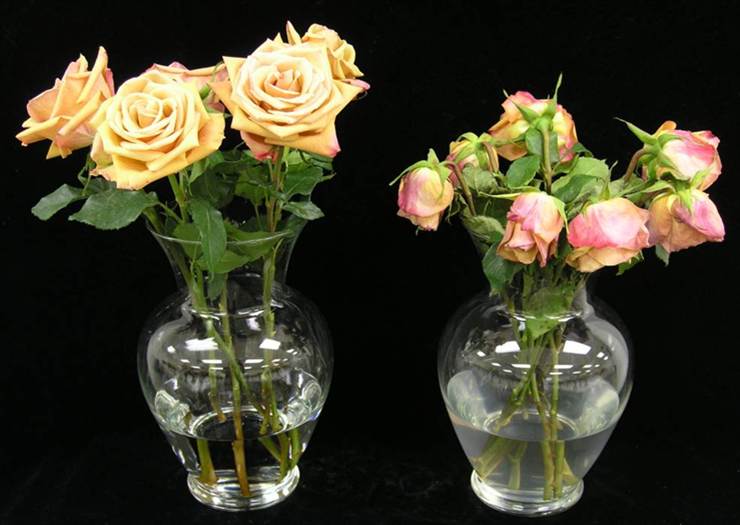
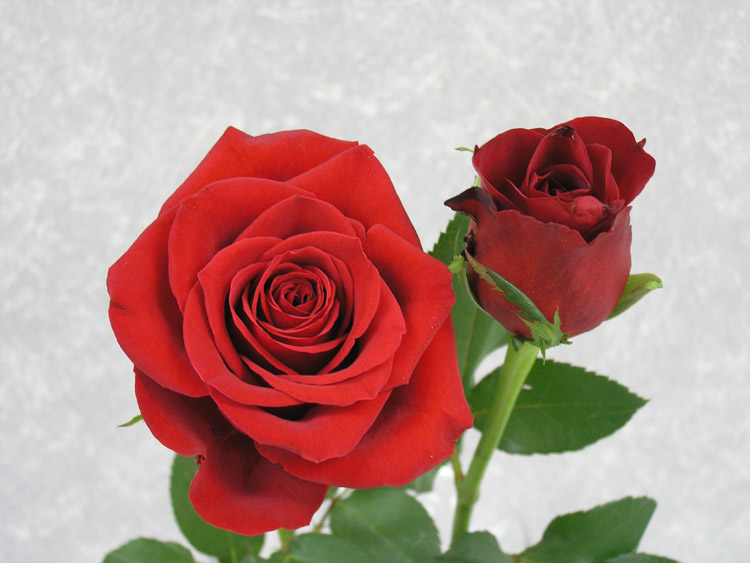
*Product availability depends upon geographical region. Check here for more information.